A thumb rule in civil engineering is a general guideline or rule of thumb used to make decisions or estimates quickly. It is not a precise calculation, but a rough approximation based on experience and knowledge.
Examples of thumb rules include estimating the cost of a project using the project’s square footage, estimating soil bearing capacity using grain size or the size of gravel, and estimating the size of a beam using the span of the structure.
Civil engineering is a diverse field that involves the design, construction, and maintenance of various infrastructure projects. As engineers tackle complex challenges, they often rely on thumb rules, which are simple, time-tested guidelines that provide quick and approximate solutions to common engineering problems.
Understanding Thumb Rule in Civil Engineering
Table of Contents
What are Thumb Rules?
Thumb rules are simplified guidelines that civil engineers use to make quick estimates and decisions during the initial stages of a project.
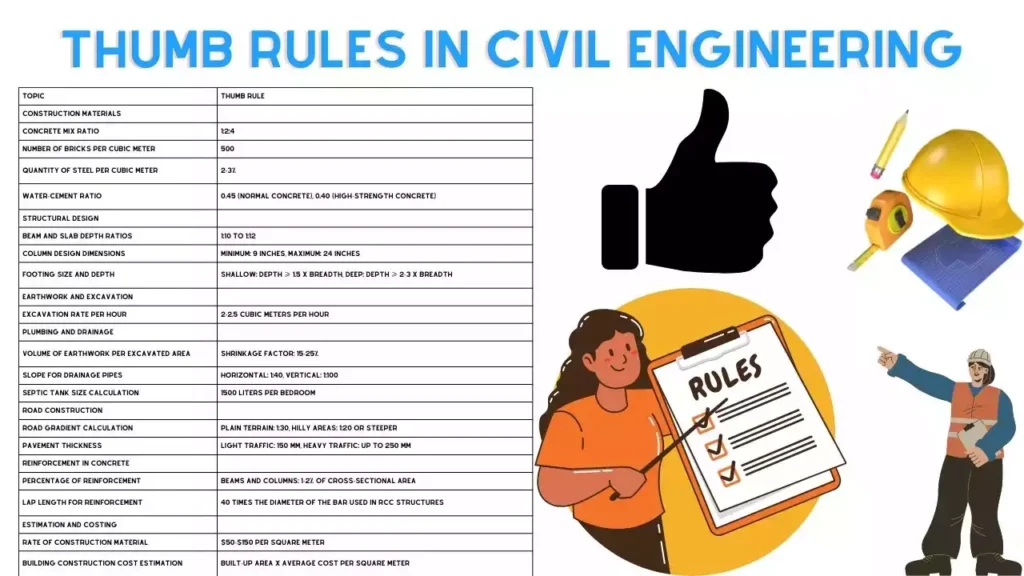
These rules are based on experience and practical knowledge, allowing engineers to perform calculations efficiently without the need for complex mathematical equations.
Why are Thumb Rules Important in Civil Engineering?
Thumb rules play a vital role in civil engineering as they help engineers quickly assess the feasibility of a project and plan accordingly. During the initial stages, engineers often need approximate values for various parameters, and thumb rules provide those values with reasonable accuracy.
Topic | Thumb Rule |
---|---|
Construction Materials | |
Concrete Mix Ratio | 1:2:4 |
Number of Bricks per Cubic Meter | 500 |
Quantity of Steel per Cubic Meter | 2-3% |
Water-Cement Ratio | 0.45 (normal concrete), 0.40 (high-strength concrete) |
Structural Design | |
Beam and Slab Depth Ratios | 1:10 to 1:12 |
Column Design Dimensions | Minimum: 9 inches, Maximum: 24 inches |
Footing Size and Depth | Shallow: Depth ≥ 1.5 x Breadth, Deep: Depth ≥ 2-3 x Breadth |
Earthwork and Excavation | |
Excavation Rate per Hour | 2-2.5 cubic meters per hour |
Volume of Earthwork per Excavated Area | Shrinkage Factor: 15-25% |
Plumbing and Drainage | |
Slope for Drainage Pipes | Horizontal: 1:40, Vertical: 1:100 |
Septic Tank Size Calculation | 1500 liters per bedroom |
Road Construction | |
Road Gradient Calculation | Plain Terrain: 1:30, Hilly Areas: 1:20 or steeper |
Pavement Thickness | Light Traffic: 150 mm, Heavy Traffic: Up to 250 mm |
Reinforcement in Concrete | |
Percentage of Reinforcement | Beams and Columns: 1-2% of Cross-Sectional Area |
Lap Length for Reinforcement | 40 times the diameter of the bar used in RCC structures |
Estimation and Costing | |
Rate of Construction Material | $50-$150 per square meter |
Building Construction Cost Estimation | Built-up Area x Average Cost per Square Meter |
Thumb Rules for Construction Cost Estimates
Thumb Rule | Estimated Cost Range (in USD) per Unit/Area |
---|---|
Cost per Square Foot/Meter | $100 – $200 |
Cost as a Percentage of Land Value | 70% – 80% of total land value |
Cost per Bedroom | $10,000 – $20,000 per bedroom |
Cost per Unit | $50,000 – $100,000 per unit |
Cost of Major Systems | HVAC: $15,000 – $30,000, Electrical: $10,000 – $20,000, Plumbing: $8,000 – $15,000 |
Cost per Floor | $50,000 – $100,000 per floor |
Cost as a Percentage of Existing Building Value | 50% – 60% of current building value |
Cost of Site Preparation | $5,000 – $20,000 |
Cost per Parking Space | $3,000 – $10,000 per parking space |
- Cost per Square Foot/Meter: This thumb rule estimates the construction cost based on the area of the building in square feet or square meters. The range provided, for example, $100 – $200 per square foot/meter, indicates that the cost can vary depending on factors such as building type, location, materials used, and finishes. To get an approximate cost estimate using this rule, multiply the total area of the building by the cost per square foot/meter.
- Cost as a Percentage of Land Value: This thumb rule suggests that the construction cost might be around 70% – 80% of the total land value. It assumes that the value of the land is a significant factor in determining the construction cost. To estimate the construction cost using this rule, multiply the land value by the percentage range provided (e.g., 70% or 80%).
- Cost per Bedroom: This thumb rule is commonly used for residential projects. It estimates the cost based on the number of bedrooms in the house. The provided range, for example, $10,000 – $20,000 per bedroom, gives an idea of the cost associated with each bedroom. To use this rule, multiply the number of bedrooms by the cost per bedroom.
- Cost per Unit: For multi-unit residential or commercial projects, this thumb rule estimates the cost per unit (apartment, office, etc.). The range given, for instance, $50,000 – $100,000 per unit, provides an approximate cost per unit. To calculate the total cost, multiply the number of units by the cost per unit.
- Cost of Major Systems: This rule involves estimating the cost of major systems in the building, such as HVAC (Heating, Ventilation, and Air Conditioning), electrical, and plumbing. The provided ranges give an idea of the potential costs for each system. For the overall estimate, sum up the costs of all the major systems.
- Cost per Floor: For taller buildings with multiple floors, this thumb rule estimates the cost per floor. The range given (e.g., $50,000 – $100,000 per floor) indicates the potential cost for each additional level. To get the total cost, multiply the number of floors by the cost per floor.
- Cost as a Percentage of Existing Building Value: This rule is relevant when renovating or adding to an existing building. It suggests that the cost of the new work may be around 50% – 60% of the current value of the building. To estimate the cost, multiply the current building’s value by the percentage provided.
- Cost of Site Preparation: For projects requiring site preparation, such as clearing the land, grading, or other pre-construction activities, this rule estimates the associated cost. The range given (e.g., $5,000 – $20,000) provides an idea of the potential expenses for site preparation.
- Cost per Parking Space: This thumb rule is specifically for parking structures. It estimates the cost per parking space, which can vary depending on factors like location and construction complexity. To estimate the total cost, multiply the number of parking spaces by the cost per parking space.
Thumb Rules for Construction Materials
Concrete: Cement, Sand, and Aggregate Ratios
One common thumb rule for concrete mix design is the 1:2:4 ratio, which means one part cement, two parts sand, and four parts aggregate by volume. This ratio is often used for general construction purposes.
Concrete Mix | Cement : Sand : Coarse Aggregate |
---|---|
M5 | 1 : 5 : 10 |
M7.5 | 1 : 4 : 8 |
M10 | 1 : 3 : 6 |
M15 | 1 : 2 : 4 |
M20 | 1 : 1.5 : 3 |
M25 | 1 : 1 : 2 |
- M5 Mix (1:5:10): For every part of cement, use five parts of sand, and ten parts of coarse aggregate by volume.
- M7.5 Mix (1:4:8): For every part of cement, use four parts of sand, and eight parts of coarse aggregate by volume.
- M10 Mix (1:3:6): For every part of cement, use three parts of sand, and six parts of coarse aggregate by volume.
- M15 Mix (1:2:4): For every part of cement, use two parts of sand, and four parts of coarse aggregate by volume.
- M20 Mix (1:1.5:3): For every part of cement, use 1.5 parts of sand, and three parts of coarse aggregate by volume.
- M25 Mix (1:1:2): For every part of cement, use one part of sand, and two parts of coarse aggregate by volume.
Bricks: Number of Bricks per Cubic Meter
An approximate thumb rule for the number of bricks per cubic meter is around 500 bricks. This estimation may vary slightly based on the size of the bricks used.
Steel: Quantity of Steel per Cubic Meter of Concrete
A thumb rule for the quantity of steel reinforcement per cubic meter of concrete is about 2 to 3 percent of the concrete volume. This ensures the structural integrity of the concrete elements.
Structural Element | Thumb Rule for Steel Reinforcement |
---|---|
Beams and Columns | Approximately 1-2% of Cross-Sectional Area |
Slabs | Around 0.15-0.25% of Total Slab Area |
Lap Length | 40 times the Diameter of the Bar Used |
High-Strength Concrete | Water-Cement Ratio: 0.40 |
Earthquake-Prone Areas | Higher Percentage of Steel Reinforcement Required |
- For beams and columns, the thumb rule suggests using approximately 1-2% of the cross-sectional area of the member as steel reinforcement.
- For slabs, the thumb rule recommends using around 0.15-0.25% of the total slab area as steel reinforcement.
- In reinforced concrete structures, the lap length for steel reinforcement should be around 40 times the diameter of the bar used.
- For high-strength concrete, the water-cement ratio should be reduced to 0.40 to achieve better durability and strength.
- The percentage of steel reinforcement is typically higher in earthquake-prone areas to enhance the structural stability and resistance to seismic forces.
Water: Water-Cement Ratio
Maintaining an appropriate water-cement ratio is crucial for concrete strength. A thumb rule suggests a water-cement ratio of 0.45 for normal concrete and 0.40 for high-strength concrete.
Concrete Type | Water-Cement Ratio Thumb Rule |
---|---|
Normal Concrete | 0.45 |
High-Strength Concrete | 0.40 |
- For concrete with a higher water-cement ratio, the mix will be more workable, making it easier to place and compact. However, it may lead to a decrease in concrete strength and durability.
- On the other hand, a lower water-cement ratio in high-strength concrete results in improved compressive strength and durability, but the mix becomes less workable, requiring more effort during placement and compaction.
- The water-cement ratio is crucial in preventing the formation of cracks and ensuring long-term durability of concrete structures.
- In situations with adverse weather conditions, such as hot and dry environments, a lower water-cement ratio is recommended to minimize shrinkage and cracking.
- In earthquake-prone regions, using a higher water-cement ratio can provide better resistance to seismic forces by increasing the ductility of the concrete.
- It’s important to follow the recommended water-cement ratio and avoid adding excess water during the concrete mixing process, as this can significantly impact the final properties of the concrete.
Thumb Rules for Structural Design
Beam and Slab Depth Ratios
For reinforced concrete beams and slabs, a common thumb rule suggests a depth-span ratio of 1:10 to 1:12. This ensures the beams and slabs can handle the applied loads effectively.
Beam and Slab Span Length | Recommended Depth Ratio |
---|---|
Short Span (Light Loads) | 1:10 |
Long Span (Heavy Loads) | 1:12 |
For example, if the span length of a beam is 5 meters, the depth of the beam should be around 0.5 to 0.42 meters. Similarly, for a slab with a span length of 6 meters, the depth of the slab should be approximately 0.5 to 0.6 meters.
These depth ratios are commonly used in the design of beams and slabs in reinforced concrete structures to ensure structural efficiency and adequate load-bearing capacity.
Column Design: Minimum and Maximum Dimensions
A thumb rule for column design states that the minimum dimension of a column should not be less than 9 inches, and the maximum dimension should not exceed 24 inches.
Column Type | Minimum Dimensions | Maximum Dimensions |
---|---|---|
All Columns | Approximately 9 inches (225 mm) | Approximately 24 inches (600 mm) |
- The minimum dimensions of a column, typically around 9 inches (225 mm), are essential to ensure that the column can withstand the applied loads without experiencing excessive deflection or failure.
- Columns with smaller dimensions may not provide sufficient strength and stability, leading to structural instability and compromised safety.
- The maximum dimensions of a column, commonly around 24 inches (600 mm), are considered to optimize the use of materials and space while providing adequate load-bearing capacity.
- Columns with larger dimensions may result in increased material costs and reduced usable space without significant improvements in load-carrying capacity.
- The dimensions of columns depend on various factors, including the type of structure, the magnitude and distribution of loads, and the design codes and standards applicable in a particular region.
- Columns in high-rise buildings may have larger dimensions to accommodate the higher loads and maintain structural integrity.
- In reinforced concrete structures, the dimensions of columns play a critical role in providing proper cover to the reinforcement, preventing corrosion and ensuring the durability of the structure.
- The design of columns should consider factors such as earthquake resistance, fire resistance, and serviceability requirements to meet the specific demands of the project.
- For optimal column design, it is essential to engage a qualified structural engineer who can perform detailed analysis and calculations based on specific project requirements and safety considerations.
Footing Size and Depth
Thumb rules for footing design propose that the depth of the footing should be at least 1.5 times the breadth for shallow footings and 2 to 3 times the breadth for deep footings.
Footing Aspect | Thumb Rule |
---|---|
Shallow Foundation | Depth approximately 1 meter (3 feet) below the ground surface. Width approximately 3 times the width of the column or wall it supports. |
Deeper Foundations | Depth varies based on soil conditions and load-bearing capacity. Consult a qualified geotechnical engineer for precise determination. |
Width of Footing | For single column or wall, width is generally taken as 2 times the width of the column or wall it supports. |
Depth of Footing | Minimum depth is 1.5 times the width of the footing for shallow foundations. For isolated footings supporting columns, minimum thickness is typically 150 mm (6 inches). |
Expansive Soils | Increase footing depth to prevent potential heave or settlement due to soil moisture changes. |
Footing on Slopes | Increase depth on the lower side to counteract slope-induced lateral forces. |
Heavy Load Footings | Larger sizes and depths may be required for footings supporting heavy loads in industrial structures or high-rise buildings. |
Special Foundations | Machine foundations and other specialized footings should be designed based on dynamic forces and soil properties. |
Site-specific Factors | Consider water table level, presence of nearby trees, and adjacent structures when determining footing size and depth. |
The width of the footing for a single column or wall is generally taken as 2 times the width of the column or wall it supports. This provides adequate stability and prevents excessive settlement.
The depth of the footing should be at least 1.5 times the width of the footing for shallow foundations. This helps to distribute the load over a larger area and minimize settlement.
For isolated footings supporting columns, the minimum thickness of the footing is typically taken as 150 mm (6 inches). However, this may vary based on the structural loads and soil conditions.
In areas with expansive soils, the depth of the footing may need to be increased to prevent potential heave or settlement due to soil moisture changes.
For footing design on slopes, the depth of the footing should be increased on the lower side to counteract the effect of slope-induced lateral forces.
Footings supporting heavy loads, such as in industrial structures or high-rise buildings, may require larger sizes and depths to handle the increased loads and moments.
The size and depth of the footing can also be influenced by factors such as the water table level, presence of nearby trees, and adjacent structures.
For machine foundations, the depth is generally determined based on the dynamic forces generated by the machine and the soil properties to avoid excessive vibrations.
Thumb Rules for Earthwork and Excavation
Excavation Rate per Hour
A thumb rule for excavation states that one worker can typically excavate around 2 to 2.5 cubic meters of soil per hour.
Excavation Equipment | Excavation Rate per Hour (Approx.) |
---|---|
Manual Labor and Small Excavators | 30 – 50 cubic meters per hour |
Medium-sized Excavators | 50 – 80 cubic meters per hour |
Large Excavators with Skilled Operators | 80 – 120 cubic meters per hour or more |
The excavation rate per hour can be affected by the type of soil or material being excavated. Soft and loose soils may be easier to excavate, leading to a higher rate, while dense or rocky soils may slow down the excavation process.
For small-scale excavation tasks using manual labor or small excavators, the rate may be around 30 to 50 cubic meters per hour.
Larger excavation projects using heavy machinery and skilled operators can achieve higher rates, ranging from 80 to 120 cubic meters per hour or more.
The type and size of the excavation equipment also play a significant role in determining the rate. Larger and more powerful excavators can move larger volumes of material in a shorter time.
The efficiency and experience of the excavation crew are crucial factors in achieving the desired excavation rate. Well-trained operators can optimize the equipment’s performance and minimize downtime.
In urban areas or congested sites, the excavation rate may be slower due to space constraints, safety measures, and the need for careful excavation to avoid damage to nearby structures.
Groundwater and adverse weather conditions can also impact the excavation rate, as they may require additional measures to control water ingress or prevent soil instability.
The type of excavation, such as trench excavation, foundation excavation, or mass excavation for earthworks, can influence the rate as well.
Excavation rates for specific materials, such as rock excavation or excavation for specific utilities like pipelines, may have different rates due to their specific challenges and requirements.
Volume of Earthwork per Excavated Area
A rough estimation for earthwork volume is to consider a shrinkage factor of 15 to 25% when calculating the volume of soil after excavation.
Thumb Rules for Plumbing and Drainage
Slope for Drainage Pipes
An essential thumb rule for the slope of drainage pipes suggests a minimum slope of 1:40 for horizontal drainage and 1:100 for vertical drainage.
Septic Tank Size Calculation
The thumb rule for septic tank size is to consider a capacity of 1500 liters per bedroom for residential buildings.
Thumb Rules for Road Construction
Road Gradient Calculation
A common thumb rule for road gradient states that for plain terrain, the road gradient should be around 1:30, while in hilly areas, it can be 1:20 or steeper.
Pavement Thickness
Thumb rules suggest a pavement thickness of 150 mm for roads with light traffic and up to 250 mm for heavy traffic.
Thumb Rules for Reinforcement in Concrete
Percentage of Reinforcement in Beams and Columns
Thumb rules propose that the percentage of steel reinforcement in beams and columns should be around 1 to 2% of the cross-sectional area.
Lap Length for Reinforcement
A thumb rule for the lap length of reinforcement bars is 40 times the diameter of the bar used in RCC (Reinforced Cement Concrete) structures.
Thumb Rules for Estimation and Costing
Rate of Construction Material per Square Meter
A common thumb rule for construction material rates suggests that the cost of construction materials per square meter ranges from $50 to $150, depending on the quality and location.
Cost Estimation for Building Construction
A rough estimation for building construction cost can be calculated by multiplying the built-up area with the average cost per square meter, including material and labor charges.
Conclusion
Thumb rules serve as valuable tools for civil engineers, providing quick and useful estimates during the initial stages of projects. These simplified guidelines expedite decision-making processes and help in the efficient planning of construction activities. However, it is crucial to use thumb rules with caution and verify their applicability in specific project contexts.
Frequently Asked Questions
Can thumb rules be applied to all construction projects?
Thumb rules are useful for quick estimates but may not be suitable for complex or critical projects. Engineering judgment is necessary to determine their suitability.
Are thumb rules accurate for structural design?
Thumb rules provide approximate values and should be used as a starting point. Detailed calculations and analysis are essential for precise structural design.
How can I ensure the reliability of thumb rules?
Experience and validation from previous projects can enhance the reliability of thumb rule-based estimates.
Is it essential to cross-check thumb rule-based calculations?
Yes, cross-checking with detailed calculations and consulting experienced engineers is advisable for critical projects.
Can thumb rules replace engineering calculations?
Thumb rules are meant to supplement engineering calculations, not replace them. Proper engineering analysis is indispensable for safe and robust construction.
How do I use thumb rules in construction?
To use thumb rules, simply apply the appropriate rule to the specific parameter you want to estimate. For example, to estimate concrete quantity, use the concrete mix ratio thumb rule.
What is the thumbrule for concrete mix ratio?
The thumb rule for concrete mix ratio is to use the standard mix proportions like 1:2:4, 1:1.5:3, etc., for different grades of concrete, depending on the required strength and application.
What is the excavation rate per hour thumb rule?
The excavation rate per hour thumb rule varies based on the equipment used and site conditions. Typically, it ranges from 50 to 100 cubic meters per hour for medium to large excavators.
How can I estimate the volume of earthwork per excavated area using thumb rules?
Multiply the area of the excavated surface (length × width) by the average depth of excavation to estimate the volume of earthwork in cubic meters or cubic yards.
Can I solely rely on thumb rules for construction projects?
Thumb rules should only be used as initial estimates. For accurate and safe construction, it is crucial to engage qualified engineers and follow standard engineering practices.